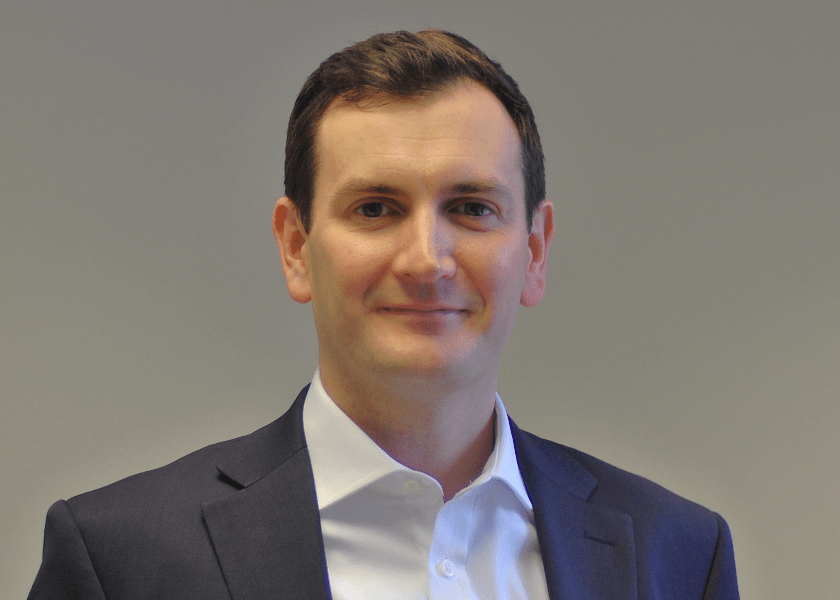
Unwrapping plastic
Ross Moloney, CEO of LEEA (Lifting Equipment Engineers Association) welcomes an initiative to reduce packaging waste in global supply chains.
Attitudes towards plastic are changing – jolted by images of oceans full of floating plastic waste and the terrible impact it is having on sea life. Almost a third of the 78 million tonnes of plastic packaging produced worldwide annually is left to flow into our oceans, according to a study undertaken by the World Economic Forum, the Ellen MacArthur Foundation and McKinsey and Company. The study goes on to suggest that this is the equivalent of pouring one garbage truck of plastic into the ocean every minute – and if this continues, by 2050 there could be more plastic than fish in the world’s oceans.
So I was encouraged to read about REID Lifting eliminating all single use plastics from packaging its davits and gantries for shipping both overseas and in the UK. The company has switched to using sustainable and recyclable rigid cardboard containers for its product range, which are easy to stack and easy to ship. As well as protecting the products during transportation, the containers can be stacked, thus giving an additional benefit of enabling more products to be packed into each container and more containers onto each lorry, resulting in a reduction in empty space. This in turn leads to a reduced carbon footprint for products as they are exported to the US and around the world.
Around a quarter of what businesses ship is empty space, according to research from packaging company DS Smith. This unnecessary ‘shipping of air’ around the globe is reckoned to add up to the equivalent of the annual emissions of a country like Belgium.
It will require innovation to deal with these issues and this is a welcome initiative from a LEEA member company operating in global markets. Reducing plastic waste and empty space during shipping is not only environmentally considerate – it is also cost effective.
Regulations and legislation globally will play a significant role in driving for new packaging practice. For example, the EU waste directive includes targets for packaging. By 2030, 70% of packaging should be recyclable. However, consumer pressure will have a greater immediate impact. As individual organisations seek to improve their own environmental credentials they will be looking at suppliers who can comply with their sustainability requirements. This is becoming an important part of a procurement department’s supply chain audit.
Given the high volumes of products and parts being shipped around the global lifting industry, widespread reduction in plastic packaging in our sector would be a significant contribution to reducing the waste problem. Like all industries we must look at steps to develop our sector in a sustainable fashion. We must demonstrate to supply chains in end user markets that we are addressing these concerns.
Gravity doesn’t recognise different countries, languages or legislation. It’s the same wherever you are in the world, and in this sense ours is perhaps the most globalised of all industries. Reducing packaging waste and carbon footprints is an international issue, making it particularly pertinent to the highly global lifting sector. It underlines why it is vital to possess a truly global outlook and the importance of raising standards globally in all aspects of our sector.