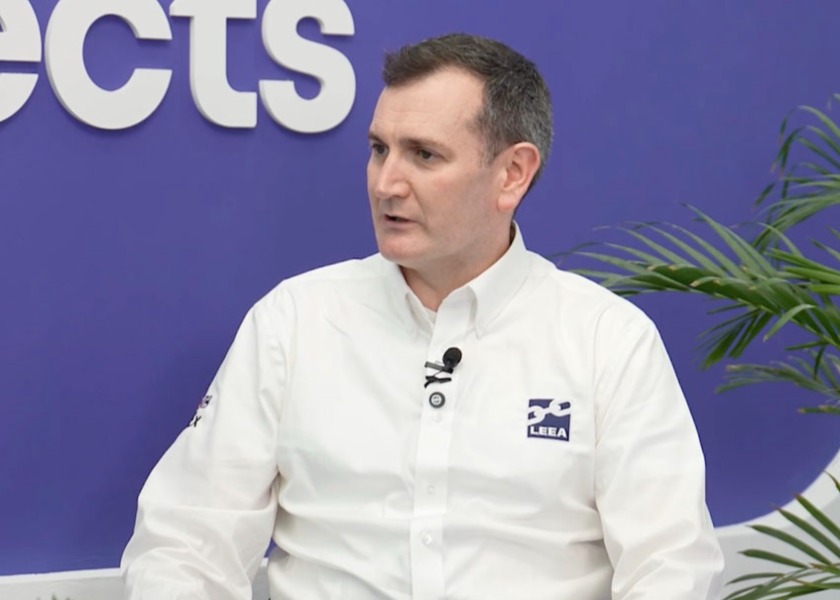
Revealing the state of the Lifting Industry
Dr Ross Moloney, CEO of LEEA) highlights the findings contained in the important new State of the Lifting Industry Report, launched during GLAD2025.
Ours is a dangerous industry, if not THE most dangerous. As the global association for the Lifting Industry, LEEA aspires to make it safe. We aim to fight gravity not just to lessen or reduce, but to eliminate to zero all accidents, injuries and fatalities that happen in our industry. Achieving that goal depends on the competence, behaviours and confidence of the people carrying out this safety-critical work. We must therefore ensure they are equipped with the right skills at the right time.
To find out where our industry stands in terms of these issues, LEEA conducted the world’s largest research survey of our industry in April and May. The findings have been published in our State of the Lifting Industry Report, issued as part of our ‘Shining a light on the industry that holds the world up’ campaign, launched during GLAD2025. This important survey, which garnered almost 400 responses from over 50 countries, helps us speak with even greater authority about some of the things we are observing in an industry that is vital for supporting the global economy. By revealing the extent of skill challenges, our hope is that the report will be a call to arms for the sector, to ensure lifting operators have the skills they need to stay safe at work.
Accidents, injuries and fatalities
Here is the reality: across all of industry, not just lifting, 374 million people globally have a non-fatal accident at work that is significant enough to result in an absence from the job of four days or more. Gathering global statistics in this area is difficult due to the different ways numbers are collected. However, to further illustrate the problem, in 2024, the UK recorded 138 people suffering fatal accidents, which involved either simply falls from height or being struck by a falling object to being trapped by collapse. Those accidents accounted for 62% of all UK workplace fatalities.
As for non-fatal injuries: every single day in the UK alone, there are 300 accidents relating to either falling from height or being struck by objects. On average, a fall from height results in the next 15.3 days of work being missed. Being struck by something falling means it takes at least a week, on average, before a return to work. These are numbers, derived from accepted governmental data, make clear the personal as well as the economic cost of accidents, which feeds back to issues raised in the survey including skills gaps, training and recruitment.
Recruitment, retention and skills gaps
Where the next generation of staff is coming from is clearly keeping members awake at night. The survey uncovers a useful nugget of information here: we know many of the reasons why people leave, such as the challenging environment or the unsociable hours, but our research reveals that a trained member of your team is more likely to stay with you than a non-trained member. Untrained staff tend not to feel valued and lack confidence about performing tasks they don’t feel sufficiently skilled to fulfil. Employers need to see training as a crucial staff retention factor. When you invest in your staff, they feel invested in, and that will make them stay.
Finding the right people to work for you will inform the training that you carry out or seek from an organisation, such as LEEA. Knowledge of relevant laws and regulations is the most common skill lacking, according to the survey, yet in our industry this knowledge is crucial to be legally compliant, and to understand standards and what best practice looks like.
Ours is an industry as old as time, yet the way we do things is changing so skills needs are changing quickly, as 90% of our respondents report. The feedback is that AI in digitalization is not something for the future, it’s already upon us and that's a fundamental shift.
The value of training
We know that ours is a risky and a dangerous industry. At LEEA, we believe that skills equals competence, equals safety. Where there is a lack of annual (at least) training, we worry about the ongoing skills and competence of staff. Nearly half (46%) of operators in our industry lack ongoing training. We need to ensure there is bite size learning allowing people to be not just legally compliant, but also feel motivated to stay at the employer and understand what best practice looks like.
Cost of training is an issue. LEEA, which operates as a not-for-profit organisation, is here to correct that market failure by making training as accessible as possible, in terms of opportunity and price.
We’ve identified that managers don’t feel they have the time to arrange training. This could be due to not understanding the importance of training and that it is an investment. Recent data suggests that every pound spent on health and safety training in our industry results in a saving of £12. That’s an impressive return. Also, training might not be high enough on today’s ‘to do list’. If these are your training challenges, get in touch with LEEA and let us support you.
Seven out of ten (71%) in our industry, on an anonymous basis, believe that they could be doing more when it comes to training their staff. This is alarming because we know the direct correlation between safety and training, as quote from the survey says: “The easiest way to deal with making people more competent is to invest in training. It’s a cheap and effective safety option.”
Regional differences
Another interesting reveal from the survey is the different challenges by region. Australia, New Zealand and the UK have older workforces characterised by experience, whereas other regions have a younger workforce, something that might be wished for by UK & ANZ employers dealing with the challenges associated with retirement and regenerating the workforce.
Given younger people tend to be much more comfortable with digital solutions, while the older generation continue to value in person, classroom-based training, managing knowledge share between the two is something that needs considering.
LEEA members lead the way
We are delighted to find from the survey that LEEA members are less likely to report skills gaps. We believe that that is because they understand the relationship between skills and safety and therefore invest in skills and in their staff. The data shows it comprehensively. For example 45% have promoted their current training practices to applicants compared to 33% of non- members. LEEA members are simply more likely to train their staff and they are much more on top of the habitual skilling of their staff. While they may well have challenges in recruitment, as everybody in the industry does, they are better informed about what it is that they're actually looking for.
This reflects how LEEA members seek to be the best in class because they care about standards, they care about their people, they care about their solutions, their product and their customer. They are always seeking to improve and want to make workplaces and people safer. But we represent the high barrier. For anyone seeking to buy or use lifting equipment, I’d encourage you to look for a LEEA member because of these values and the measures that they put in place to ensure that their staff are trained, competent and skilled.
To fully understand what is happening in the Lifting Industry, the State of the Lifting Industry Report makes essential reading for individuals, businesses, stakeholders and policymakers. It is available to download for free on a new LEEA microsite leealiftingfutures.com.