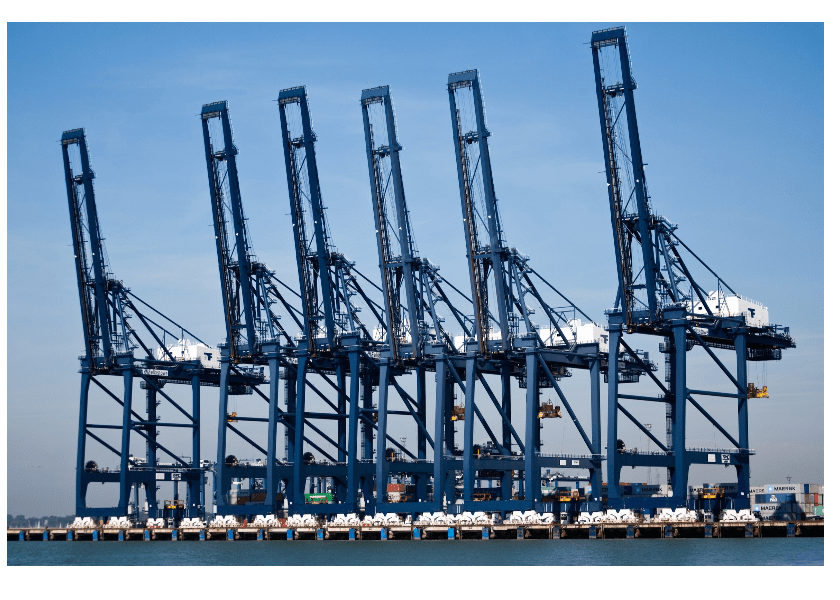
Preventing port crane failure through rope monitoring
Greater awareness of condition monitoring of wire ropes using magnetic head technology is required to avoid the risk of catastrophic port crane failure, writes Denis Hogan, Performance and Special Projects Manager at LEEA (the Lifting Equipment Engineers Association), and Keith Tonge, LEEA Technical Officer.
In May 2017 a port side crane in Falmouth Docks failed without any warning leading to its jib crashing down to earth. Fortunately no significant injuries were incurred in this major incident. While as yet, no official cause has been published, the immediate prohibition notice issued by the HSE (Health and Safety Executive) describes a failure to ensure that lifting equipment is maintained in an efficient state, efficient working order and good repair. The need for regular maintenance and inspection of lifting equipment at ports is critical. PUWER 1998 [3] Regulation 5 requires employers to ensure that cranes are maintained in an efficient state, in efficient working order and in good repair. The Health and Safety at Work etc. Act 1974 [1] sets out a general duty requiring that work equipment is maintained so that it is safe. Thorough examination of cranes is required by LOLER 1998 Regulation 9 in the following circumstances.
Regular inspection on the structure of a port crane, its sheaves, the jib and the slew mechanism are just some of the areas of focus for maintenance programmes carried out by port operators. But wire ropes should also be a key part of the programme, yet too often this element is overlooked.
Without proper maintenance and inspection of the crane rope, there is a risk of internal degradation that can lead to the wire rope giving way completely with catastrophic results.
Fortunately condition monitoring of ropes on a crane is coming to the fore. The ISO 4309 standard published at the end of 2017, which provides the international inspection and rejection criteria for crane ropes, now includes non-destructive testing of steel wire rope as an important element to ensure that the condition of the rope is monitored from cradle to grave.
This allows operators to predict the point where the wire rope actually needs to be changed allowing planned preventive maintenance, leading to maximising uptime.
Magnetic Rope Testing (MRT) technology for the non-destructive examination of wire rope has been around since the mid-1950s, when it was developed in conjunction with the National Coal Board for checking the condition of deep shaft mining ropes. It involves running a wire rope through a magnetic head that allows an inspection right into the centre of the rope, giving clear visibility of any broken wires, voids and corrosion.
Rope manufacturers on certain products will pass the wire rope through a magnetic head during the final stage of its manufacture, when they close the strands round the core. This produces a trace showing the state of the rope when it was created and before it was installed.
By then checking on a regular basis – typically 6 months, though the period will depend upon usage of the crane – one trace can be compared with the next to observe any developing defects. When the rope gets to the point of rejection criteria, managers can plan in the change without fear of rope failure, maximising uptime in busy ports.
Now the way forward for maintenance of wire ropes installed on port cranes, MTR was not always possible in the past but advances in technology have made MTR eminently portable, and it can even become a fixture of the crane itself in some cases, allowing the rope to be constantly monitored as it is used. An MRT unit today can send a signal directly to the manager’s computer screen to give a visual representation of how the wire rope is deteriorating over time. In fact MRT technology is now considered so important that it has been incorporated into ISO 4309.
MRT has become crucial for routine monitoring of ropes in offshore applications, where minimising costly downtime is particularly critical. The technology is discussed within a guide on the condition monitoring of wire ropes in offshore installations published by the International Marine Contractors Association (IMCA), which itself is starting to drive greater awareness for using the technology in ports.
When it comes to the provision of lifting equipment maintenance and repair services it is always prudent for ports to seek out the ‘gold standard’. In addition to offering expertise on MRT and condition monitoring of wire ropes, LEEA members are structured to provide specialised repair and maintenance as well as the inspection function, as separate parts of a one stop shop, in compliance with HSE guidelines. This will allow ports to further mitigate risk of crane failure and to improve the management of their lifting equipment uptime, allowing them to handle growing volumes safely.
For further information contact LEEA: mail@leeaint.com or visit www.leeaint.com.