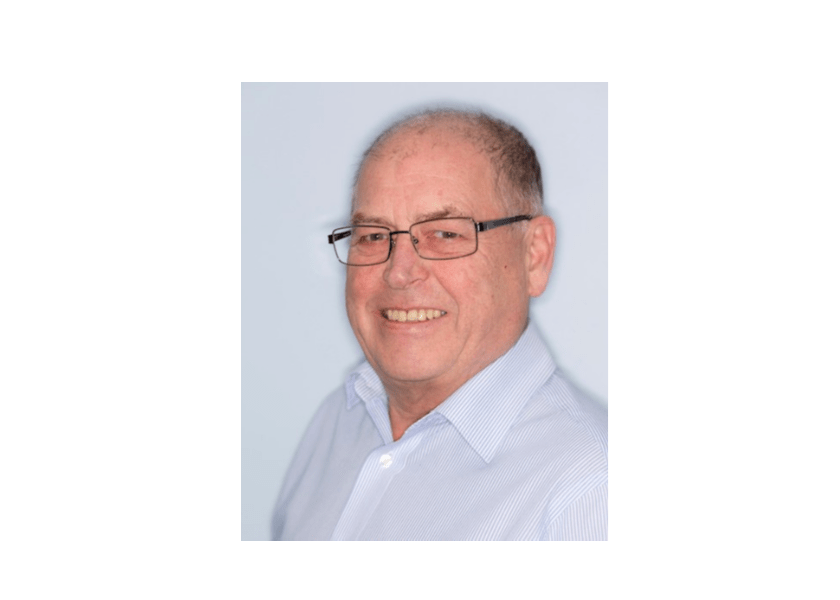
Look inside the rope
By giving visibility right through to a wire rope’s core, Magnetic Rope Testing (MRT) can play an vital role in improving lifting sector safety, says Denis Hogan, Performance and Special Projects Manager at LEEA.
Many operations still rely only on visual inspection of wire ropes. However, plant engineers need to be made aware of the existence of Magnetic Rope Testing (MRT) and the crucial role it can play in maintenance – particularly on high integrity cranes that are being used intensively throughout their working life. MRT gives plant engineers the ability to predict the life expectancy of the rope, allowing them to plan replacement in a just-in-time manner, without the need for bulky wire rope to be consuming space in stock.
MRT is the means to see into the heart of wire rope used on cranes and other steel wire rope and cable products, such as mast stay and bridge cables, in order to detect any deterioration that might have occurred in service.
The MRT method involves passing the rope through a permanent magnet. This sets up an electromotive force, which is picked up with electronic sensors that can detect any breaks in the rope or any corrosion that occurs throughout the section of the rope, which is known as Loss of Metallic Area (LMA). There are different MRT equipment manufacturers but the method is exactly the same with each one.
To examine the core of the rope under normal examination, without MRT, requires a special tool to open the rope’s strands. But this still only gives visibility of a small percentage of the rope’s length. On multi-strand crane ropes, you can never see the core because the multiple layers can’t be opened up due to the underlying layers being laid in the opposite direction to the outer strands.
For high integrity cranes, particularly those used offshore, wire rope manufactures will use MRT to produce a ‘baseline’ as a ‘birth certificate’ for a length of wire rope. So when it enters service, the engineer knows precisely what that rope is like at the outset and can then accurately monitor any deterioration throughout its service life.
MRT was developed in the mid-1950s by the National Coal Board in conjunction with British Ropes, which went onto become Bridon Ropes (which is now Bridon Bekaert The Ropes Group). It was developed specifically for deep-shaft mine ropes used for hauling the cradles up and down, ensuring safety for people working down the coal mines.
The first machine they brought out followed exactly the same principles as I described previously but all the components were a considerable size – the recorder and oscilloscope almost filled an entire room. This remained the case with MRT equipment until the mid-1990s when the wire rope industry developed modern technology that works to exactly the same principle but is a fraction of the size, thus making it far more practical.
It is important to point out that MRT has been added to ISO 4309 Cranes – Wire ropes – Care and maintenance, inspection and discard as a method of examination of in-service cranes ropes, but only as a supplement to visual examination.
MRT is, however, a vital tool for safety and maintenance systems. I have seen a rope that outwardly looked perfectly OK, but it dropped a load because its core was completely and utterly degraded through fatigue failure. Fortunately nobody was hurt on this occasion but it could easily have resulted in a fatality. The failure would have been detected quickly had it been through MRT, preventing the risk of accident.