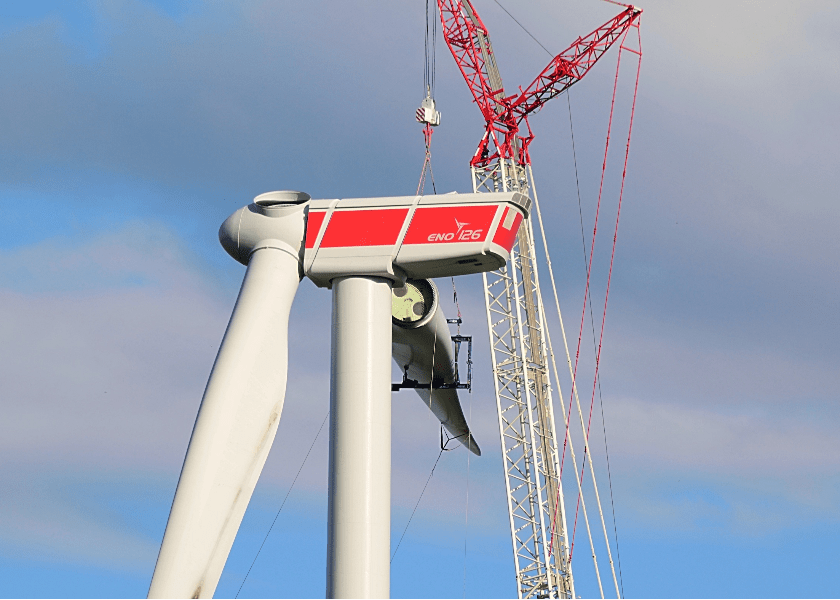
Keeping it safe and efficient when working in wind
Denis Hogan, Performance and Special Projects Manager at the Lifting Equipment Engineers Association (LEEA), highlights the regulations for working safely and efficiently with lifting equipment in the European wind energy sector.
As the wind energy sector expands, so too does its requirement for lifting equipment, for which this relatively new industry sets several challenges. Working with lifting equipment must be carried out with safety as the priority because working at height exposes people to risk. Working in the wind energy sector often adds harsh environments into the equation. This compounds the costs of maintenance in a sector where uptime is already a priority in order to maintain energy generation.
There are two key pieces of legislation that applies to all lifting equipment and accessories that may be used in the wind energy sector in Europe. The Machinery Directive polices the market in the first instance then, when the equipment is in service, the Work Equipment Directive applies to servicing, maintenance, repair and thorough examination inspection.
Given that the lifting equipment is fit for the intended purpose, having a regular maintenance programme is crucial because of the environment in which it operates – even onshore the equipment can be subjected to highly corrosive atmospheres. This will identify repairs and help maintain equipment in good working order. In addition, the equipment needs to be thoroughly examined according to the appropriate regulations.
As mentioned this is primarily the Work Equipment Directive, but it is also important to follow the subtle difference of the regulations of the country in which the equipment is operated. For example, in the UK this means LOLER (The Lifting Operations and Lifting Equipment Regulations 1998), and PUWER (Provision and Use of Work Equipment Regulations 1998).
When designing a programme for maintenance, it is vital that the risks and the conditions involved and the environment in which it operates are taken into consideration. The programme for thorough examinations may need to be at a greater frequency than is required by the Work Equipment Directive, as is the case in UK, to mitigate the risk of something going wrong.