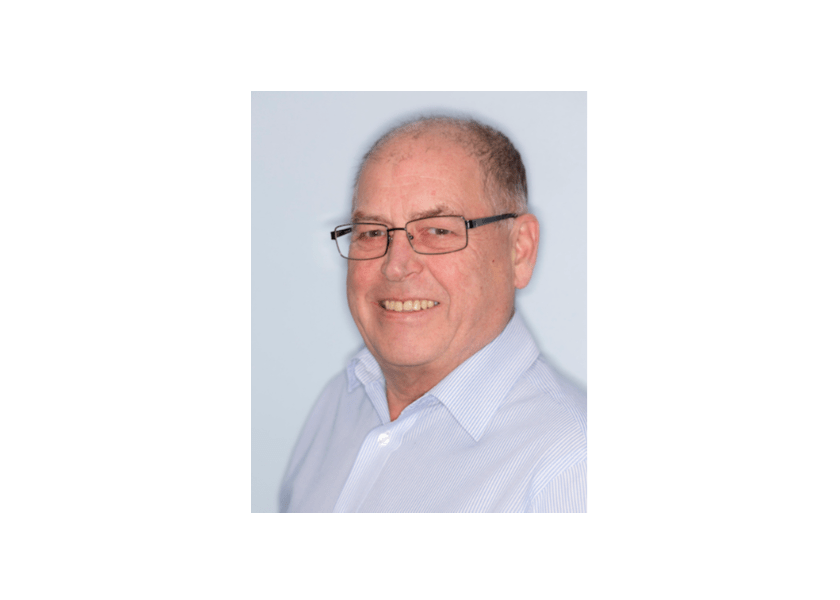
Have you got the correct documentation?
Denis Hogan, Performance and Special Projects Manager at LEEA, highlights the lifting equipment related documentation that needs to be provided by manufacturers and suppliers to assure customers of legal compliance.
Manufacturers and suppliers of lifting equipment and related inspection services are legally required or bound by product standards to provide the correct documentation to their customers. Yet there appears to be genuine confusion about what document should be provided in different circumstances.
Within Europe customers and users need assurance that the equipment supplied meets the requirements of the Machinery Directives and other legislation such as PUWER and LOLER. If the documents supplied do not correctly meet the necessary requirements, then this could place the supplier in breach of the law.
In some countries or regions outside of Europe, similar requirements for the supply and periodic inspection of lifting equipment are bound up in Federal or National legal requirements and/or within National or International standards such as the AS 3775 series for chain and AS 1418 series for cranes in Australia, ASME B30 series for cranes and below the hook accessories in the USA, ISO 4309 defining the discard criteria for crane ropes, to name but a few.
In the absence of any National legal or standards requirements, many countries or regions have adopted LOLER and PUWER supported by equipment manufactured and certified in accordance with European standards and CE marked accordingly.
Although supplying the incorrect documentation does not necessarily mean that the lifting equipment is unsafe, the customer would naturally question the competence of the people who have issued it. There are three main types of documents:
- Manufacturer’s Certificate
- EC Declaration of Conformity (Where European Standards plus LOLER & PUWER have been adopted)
- Report of Thorough Examination (sometimes referred to as a “Periodic Inspection” or a “Field Test Report”).
Manufacturers Certificate
The document that accompanies new lifting equipment was, in the past, often referred to as a ‘Test Certificate’. This document is applied in general when new items of lifting equipment were individually proof load tested to prove that they can carry the rated Working Load Limit. However, today, within European and increasingly within ISO standards, a greater emphasis is placed on quality control during manufacturing to ensure the necessary properties and requirements are met. Many below the hook lifting products are no longer individually load tested with a proof load, so the more fittingly named ‘Manufacturer’s Certificate’ has largely superseded the name ‘Test Certificate’ However, where tests are applied to the equipment during manufacture, the test results or load applied must be referred to within the Manufacturers Certificate.
The information to be contained in the Manufacturer's Certificate is compulsory and is listed within the various product standards. Any manufacturer claiming to comply with the standard must issue that document and it should include:
- The name and address of the manufacturer or his authorised representative
- The date of issue of the certificate
- A signature or other authentication
- The number (and part if applicable) of the standard
- Description of the item(s)
- Identification of the item(s).
The manufacturer must also issue the document required by legislation. In Europe, the requirements are contained in the Machinery Directive. The original Directive dates back to 1992 and there were various amendments until it was replaced completely in 2006. The most recent Machinery Directive is 2006/42/EC. In the UK the legislation that implements the Directive is: “The Supply of Machinery (Safety) Regulations 2008”.
The information required in that document is slightly different from that of the previous Directive, which is one reason why some manufacturers and suppliers are out of date.
The “responsible person” is whoever is responsible for placing the item on the market in the EEA. If the item is made in the EEA, that is the manufacturer. If it is manufactured outside of the EEA then it is the manufacturer's authorised representative, or the importer.
EC Declaration of Conformity
The Declaration must be typewritten or written by hand in block capitals and in the official community language, or languages of the country where it is supplied. The Declaration or a copy of it must accompany the item.
There is usually some overlap of information between the manufacturer's certificate and the EC Declaration of Conformity. Therefore the manufacturer may issue them as separate documents or may combine them. Either is acceptable provided the information is clear.
For example, where a name and address is shown, it should be clear whether that is the manufacturer, the manufacturer's authorised representative, the importer or the person authorised to compile the technical file.
The following information is required for the Declaration:
- Business name and full address of the manufacturer and, where appropriate, the manufacturer's authorised representative
- Name and address of the person authorised to compile the technical file, who must be established in an EEA state
- Description and identification of the machinery, including generic denomination, function, model, type, serial number and commercial name
- A sentence expressly declaring that the machinery fulfils all the relevant provisions of the Directive and where appropriate, a similar sentence declaring conformity with other Directives and/or relevant provisions with which the machinery complies.
Reports of Thorough Examination
The European Work Equipment Directive applies to all member countries and is enacted with slight differences in each member state. However, they all aimed at achieving one single goal, to ensure that their purchased work equipment is used only by trained operators, is regularly maintained, serviced & repaired and is periodically inspected to ensure its on-going fitness for purpose.
By far the most comprehensive of these rules are contained within the UK legislation the Provision and Use of Work Equipment Regulations 1998 (PUWER) and LOLER.
The UK legislation on Thorough Examination is in Regulation 9 of the Lifting Operations and Lifting Equipment Regulations 1998 (LOLER). The term “thorough examination” is used for the high-level periodic inspection to distinguish it from the more frequent in-service inspections usually made by the equipment user. It includes any tests deemed necessary as part of the examination. In this context, “test” is meant in the broadest sense and includes, for example, functional tests, electrical tests and non-destructive tests as well as load tests.
LOLER Regulation 10 requires a report of the thorough examination, which must contain the information specified in Schedule 1 of LOLER.
A major change introduced by LOLER is that a report must be issued following every thorough examination, including those where the equipment is found to be unsafe.
LOLER has replaced all the previous legislation and is now much simpler.
The report is the same for all sectors of industry and can be in any format provided it contains the necessary information.
Many countries, regions and even industry sectors outside the UK have adopted LOLER as being the “best practice” in ensuring that the lifting equipment under their control is used in a safe manner and periodically assessed to confirm its fitness for purpose. However, where LOLER has not been adopted, other legislation may apply for periodic inspection and this must also be recorded and retained on file. The content of such “Field Test” or “Periodic Inspection” reports may be very similar to those required by LOLER in which case those guidelines can easily be followed. LEEA are always happy to give their advice to members and customers of members to ensure such written records are adequate and meet in full, their local legislative requirements.
In summary,
For complete items of general purpose lifting equipment, there are only three certification documents, two of which are required by law:
- EC Declaration of Conformity, issued by the person responsible for placing the item on the market within Europe
- Report of Thorough Examination, issued by the person making the thorough examination.
The third document, the Manufacturers Certificate, is that specified by the standard to which the item is manufactured.
The contents of each of the above are clearly listed in the legislation and standards. It is simply a matter of checking documents issued or received against these lists.