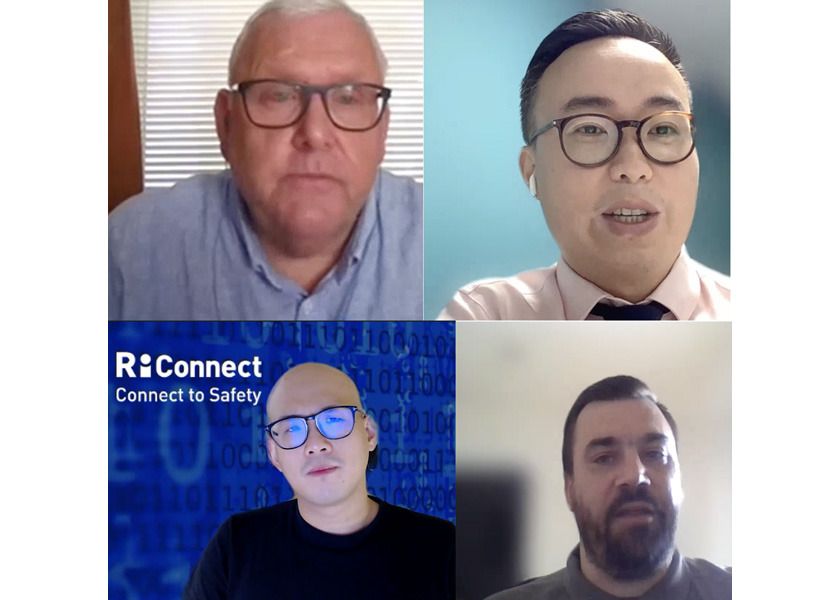
Be my Guest…special edition voxpop Plastic Free July
In a special edition of LEEA’s YouTube channel, ‘Be my Guest…’ series, Jenny Eagle speaks to several LEEA members about their sustainability efforts as part of Plastic Free July month.
Plastic Free July, organised by the Plastic Free Foundation, is a global movement that helps millions of people be part of the solution to plastic pollution, to have cleaner cities and oceans.
The challenge is to reduce single-use plastic waste every day at home, in the workplace, and in education establishments. By making small changes we can collectively make a massive difference to the environment.
Here Jenny Eagle catches up with Marcel van der Molen, Sales Director Maritime, Lankhorst Ropes, Dickson Pang, Project Manager (Westmont), Berkeley Group, Neo Kung, technical director, RiConnect and Justin Powers, Test & Inspection, Technical & Product Development Manager, Select Plant Hire.
Lankhorst Ropes is the first high performance rope maker to offer its maritime customers a rope made of Dyneema produced in the most CO2 neutral and sustainable way. Lankoforce, made of bio-based Dyneema, delivers the same performance as Lankhorst’s traditional ropes made of Dyneema, but with the added benefit of significantly increasing the sustainability of maritime mooring and towing ropes for vessel operators.
The company is committed to reducing the environmental impact of rope manufacture and use. Introducing recycle and reuse solutions, such as bio based Dyneema and post-consumer plastic waste as a feedstock, is just one of the ways Lankhorst and CirculariTeam is working to improve material sustainability and it continues to work with production partners, including DSM, and industry operators like Heerema to enhance the sustainability of the maritime and heavy lifting industries.
“Lankhorst Ropes has supplied the first ever recycled plastic HMPE (high modulus polyethylene) slings. We have delivered these to Heerema Marine Contractors and the base for the polyethylene has been ethylene extracted from recycled plastic. And we produced HMPE Dyneema heavy lift slings out of this material, and they have been used for a few projects and we are looking to reuse them for another project,” said Van der Molen.
“As a company, we want to be as circular as possible, and we know that HMPE is a material that is very difficult to recycle. Obviously, we have a big bunch of plastics around the world, and we need to do something with it. So, this is the first trial. This is the first set up and we're not there by far, but it is the first attempt. We have also have bio based which is from forestry pulp but this is also a step further.”
On talking about what kind of feedback the company had received on the trial, Van der Molen said the first concern was if the characteristics of the sling were any different from virgin material versus recycled plastic feedstock and the feedback is that there is none, it is exactly the same.
“There’s no difference in the strength or behaviour of the sling, so the end user doesn't see any difference in the characteristics of the sling,” he said.
“The project is still in its infancy. It is limited because the cost is higher. But we are in discussions with Avient (which acquired DSM Protective Materials, owner of Dyneema, in 2022) to see how we can take it one step further and pump up the volume for recycled plastics feedstock and have more slinks out in the industry based on this.”
Dickson Pang, Project Manager (Westmont), Berkeley Group, said the company is looking at recycling PPE (Personal Protective Equipment), also reusable correx recyclable schemes, to reduce packaging in general and is handing out reusable water bottles on construction sites.
Neo Kung, technical director, RiConnect, explains that as a cloud software company it helps companies in the lifting industry to be safer and more sustainable, eliminating the need to carry out checks with pen and paper.
“We help our customers install RFID tags to their equipment and mobile application, to perform these checks and generate certifications,” he said.
Justin Powers, Test & Inspection, Technical & Product Development Manager, Select Plant Hire is currently looking at alternatives to plastic inspection tags.
“Currently in our department we use a lot of plastic inspection tags. We are managing 70 to 80,000 individual lifting accessories across the UK. These are inspected every three to six months. So, we're talking hundreds of thousands of plastic inspection tags. We are currently looking at alternative tagging options and trying to drive this initiative forward, but we're not quite there yet because we're having some supply chain and cost issues and it's ultimately trying to reduce that cost to make it a more viable option to our client base. But it again, it's something ongoing that we're aware of and we're trying to work towards,” said Powers.
To see the LEEA YouTube video click here