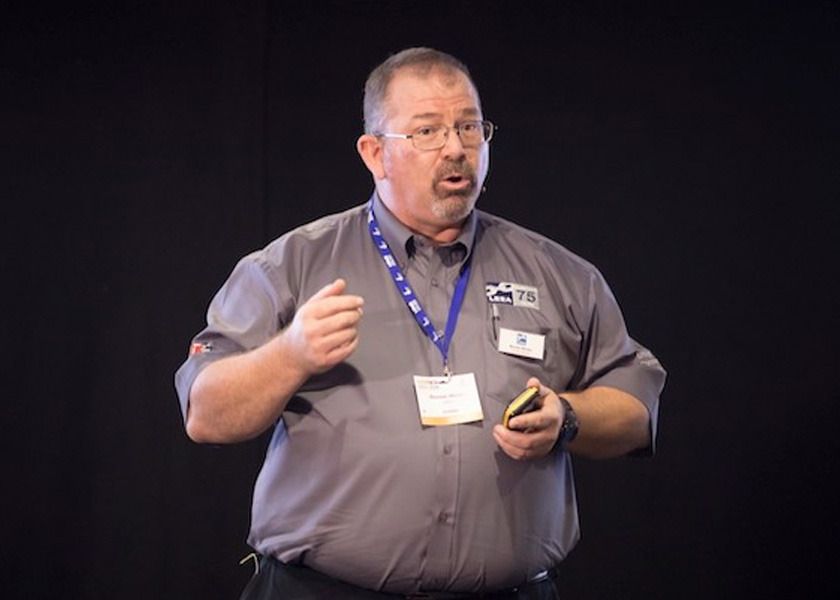
Back to lifting basics
Bernie Winter of LEEA Technical Services looks at the pitfalls that can arise when complacency sets in over lifting equipment operations, maintenance, inspections and competence.
If you are reading this article, the chances are you’re already carrying out your lifting equipment duties in accordance with the relevant legislation, but can the same be said for your end user customers?
Do you know how they actually use the equipment that you have sold or hired out to them? Can they prove that they are qualified or trained correctly on how to use a material lifter, for example?
A recent example has come to light highlighting incorrect operations and potential misuse of hired equipment. This case resulted in damage to the lifting equipment and to personal property where it was being used. The dispute over a bill in excess of £75,000 is currently with the lawyers to determine who is at fault.
In all countries around the globe, lifting is going on in every walk of life. While manufacturing requires constant lifting operations to be carried out, probably the biggest industries using lifting equipment are ports and construction. Lifting equipment in these sectors will be used for anything from positioning long spans of steel girder or pre-formed concrete sections, to off-loading bulk bags of aggregates ready for the next phase of work.
A lift can be anything from a rapid one-off event, one that is repeated hundreds of times a day – such as in product manufacturing or forklift operations – or it could be something like installing a new bridge over a minor road that is only carried out once a decade or so. Irrespective of the application or the frequency, all lifts are required to be planned in advance.
Legislation requires that lifting operations are planned by a competent person who has the correct training, knowledge and experience for the task in hand. This does not mean, however, that a competent lift planner is also competent to carry out a Thorough Inspection of the lifting equipment being used, because they must have a knowledge of how that particular piece of equipment is to be used safely.
A competent lifting equipment examiner/inspector will have the required attributes, but they will also need to know how a piece of lifting equipment should be used safely. This will enable them to identify the signs that clearly show incorrect use, which can damage the piece of equipment. It is not only lifting operation planners and lifting equipment inspectors that are required to be competent, users of the equipment are required to be competent to use it.
Equipment hire companies are regularly having to repair equipment that has been (mis)used, but competency also applies to many companies where individuals are employed as labourers by the managers and supervisors. Although it goes against legislation, many of these individuals will have had little or no training on how to use the particular piece of lifting equipment they are being exposed to and are expected to use day in, day out.
Human error
Damage usually occurs when the working load limit or safe working load has been ignored or deliberately exceeded, when additional forces have been applied to the load being lifted, or if the centres of gravity have been misjudged or not even been considered.
Modern lifting equipment is far more reliable today than was the case 20 or more years ago. Yet should an incident occur, in many cases it is the equipment in use that is the first thing to be blamed. In reality, most cases are down to human error and the causes may be traced back as far as the lift plan – or lack of one.
This is usually the case where inappropriate lifting equipment is used simply because it is close to hand and convenient or when obtaining the correct equipment for the job is both time consuming and expensive. This, in turn, increases cost and reduces profit margins. In such cases, many will try to perform the lift with what they have available.
Should the equipment be found to be the cause of an incident, it is often the case that it has been in use for a period of time since new and was not actually faulty. This is where legislation covering the use and inspection of the equipment must be followed. One of the key points is that the equipment must be used as the manufacturer intended and they are required by law to provide instructions for use with it.
Use of equipment legislation, such as PUWER in the UK, or the EU’s Directive 2009/104/EC, better known as the EU Work Equipment Directive, requires equipment to be regularly maintained to ensure it remains in a safe to use condition. This also requires frequent, and on-time examinations or inspections to be carried out, in particular, on areas of the equipment known to wear out. These inspections may be in the form of pre-use checks, interim inspections or more intense Thorough Inspections where the report is a legal requirement.
Provided this maintenance and checking system is put in place by those responsible for the equipment then, when Thorough Inspections are due, it should result in no faults being found that require repair, replacement or withdrawal due to being in an unsafe condition.
Unfortunately there are those that either forego the maintenance or interim checks and rely on the Inspection reports to tell them what needs repairing – much like a car and its MOT requirement. Up to this point if there have not been any issues then they have been lucky.
In the UK, LOLER is another piece of legislation strictly for the use and examination of lifting equipment. It sets out what is required to be put in place when planning lifting operations as well as placing stricter time frame requirements on when lifting equipment must be thoroughly examined. It also outlines what the examiner must do if they determine that a certain piece of equipment is no longer safe to use. It is similar to a car that fails its MOT, which is recorded on the government’s system as not having the MOT certificate and cannot be driven on the road until repaired. Being caught using it in this condition can result in a fine or possibly worse.
As with the use legislation, if maintenance and checking of the equipment has been carried out, then by the time a Thorough Examination is due, there should not be any issues found and the equipment may remain in use.
As with lifting operation planners and the equipment examiners, any individuals using the equipment must have the correct training and skills to ensure the equipment is used safely. Where these individuals are not trained then, in theory, it is only a matter of time until something goes wrong.
Employers have a legal obligation to ensure that their employees are trained to use equipment, so if you are selling or hiring lifting equipment, as well as supplying the safe use instructions please ask if the users have access to the LEEA Code Of Practice for the Safe Use of Lifting Equipment (COPSULE). As a safety organisation, LEEA (Lifting Equipment Engineers Association) is pleased to make this document free to download. It can be found here: LEEA Code of Practice for the Safe Use of Lifting Equipment (leeaint.com).