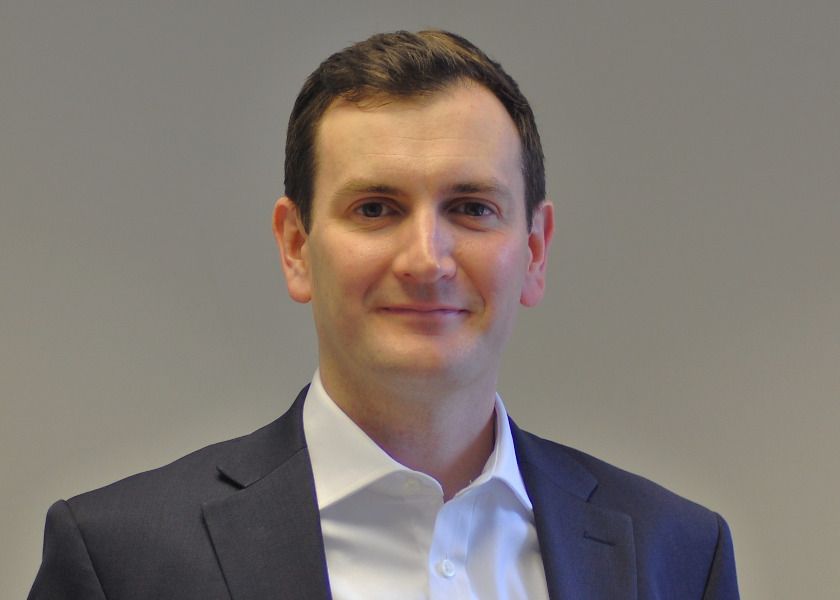
Apprenticeships: the SME employer view
Apprenticeships offer an attractive training option for smaller companies in our industry, writes Ross Moloney, CEO of the Lifting Equipment Engineers Association (LEEA).
One of the reasons why ‘old style’ apprenticeships fell into disuse was the perception that they were chiefly the province of major employers with large intakes of recruits of similar training needs that make dedicated college courses, or indeed in-house training schools, viable. Smaller companies, who arguably have a weaker position in the labour market and thus a greater need to develop their own talent, were often able to offer apprenticeships ‘on the coat tails’ as it were, of larger company provision.
As workforces have shrunk and large companies have separated or fragmented, this model has changed, but some SMEs to their credit have continued with apprenticeship schemes, and have benefited accordingly. One such in the lifting equipment industry is William Hackett Lifting Products.
Paul Davies of William Hackett explains that over the past years the company has adhered to a robust recruitment strategy. It recognises the importance of human resources to the development and success of the firm and aims to recruit people who can embrace the company’s ethos and values, and are keen to maximise their potential. The company has an open mind about intellectual status – so ‘late developers’ are welcome – but it is looking for new apprentices to show the commitment to personal development which will enable them to transition into skilled and confident operators.
William Hackett aims to be a good corporate member of its local community and so tries to offer at least one apprenticeship each year (and has achieved that over the last six years). Of the current 43 employees, seven were apprenticed at other employers, three have completed apprenticeships with the company, there are two current apprentices and two more are being recruited to start this year. In addition several school leavers have received equivalent training in-house, outside of formal apprenticeship schemes.
Just one apprentice has dropped out, having realised they had made the wrong career choice, and Paul Davies cites this as one of the advantages of apprenticeships: the flexibility to align people and roles, and to allow young people to experience different roles without everything being set in stone. At William Hackett, apprentices may be shop floor or office based, but in their first six months ‘office’ recruits will spend a lot of time on the shop floor (and vice versa) so that they get a rounded understanding of what the company really does.
Paul Davies says that apprentice entry encourages positive attitudes and expectations: “I’m starting from scratch so I can only improve”. The process of becoming part of the team may also be easier than for someone who comes in with a higher qualification but still has to start at ground level.
Economically, the relatively low, and government-supported, training cost is attractive to SMEs, and having people grow with the company is a real aid to succession planning – bringing people in at senior level from an alien external environment can be a high risk for small companies.
For the employee there are also benefits in the apprenticeship route. Economically, they are avoiding debt and generating income. For some people, formal class-based or academic learning doesn’t really work, whereas they thrive in a work-based learning environment. Getting an early foot on the ladder in their preferred role or sector can help their future career progression, and with a locally-based firm like William Hackett, trainees can develop confidence while working in their local community, often alongside family and friends.
Paul Davies is excited about the new Lifting Equipment Technician apprenticeship scheme. Hitherto, the two apprentice routes (business administration, and warehousing and storage) have been defined largely by the subjects available through local providers, with employees encouraged to pursue LEEA qualifications in addition.
As it is, 27% of employees, including members of the field sales force, and all the Directors except Finance, hold advanced LEEA qualifications. A further three are in the Foundation stage and expected to pursue advanced programmes. Paul Davies says the company is looking closely at how the new LEEA scheme aligns with the company’s needs and objectives and says: “We expect this to be an effective and efficient way of our apprentices gaining the knowledge and skills we would like to have for our and their futures.”
Watch Paul Davies explain the benefits for SMEs in offering apprenticeships during the LEEA Apprenticeship webinar presentation here: https://leeaint.com/presentation/apprenticeship-webinar-december-2021. For further information on the Lifting Equipment Technician apprenticeship and to sign up, contact ross.moloney@leeaint.com and for more details about the standard visit: www.instituteforapprenticeships.org/apprenticeship-standards/lifting-equipment-technician.